Manufacturing Solutions
Uncover the solutions DMS ERP offers to address common challenges experienced by Manufacturing companies.
Manufacturing companies often struggle with a lack of visibility and real-time insights from the shop floor. This gap can lead to inefficiencies in labor management and inventory control, directly impacting production schedules and cost efficiency. Without accurate data from the shop floor, managers specifically find it difficult to track productivity, monitor job completion times, and ensure that inventory consumption aligns with actual production needs. This lack of transparency can result in inaccuracies in timekeeping, overuse or misuse of materials, and ultimately, decreased profitability.
Solution
DMS ERP enhances visibility and provides real-time insights into shop floor operations through advanced timecard entry and direct inventory consumption functionalities tailored to your operations in our Manufacturing module.
How It Works
- Timecard Entry: DMS ERP streamlines timecard management by capturing precise labor data directly from the shop floor, reducing manual errors and ensuring accurate payroll processing. Real-time labor tracking allows managers to monitor employee productivity and efficiency, adjust workflows promptly, and optimize manpower allocation based on actual production needs.
- Direct Inventory Consumption to Work Orders: The system facilitates the direct linking of inventory consumption to specific work orders, enhancing the accuracy of material usage records. This feature ensures that each item used is automatically recorded and deducted from inventory, providing a real-time view of stock levels and usage rates. By aligning inventory data with production activities, DMS ERP helps prevent material shortages or excesses, reduces waste, and supports precise cost accounting for each job.
- Shop Floor Insights: With DMS ERP, manufacturers gain critical insights into every aspect of shop floor operations. The system provides detailed reports and analytics that help identify bottlenecks, track progress against production targets, and analyze operational efficiency. These insights empower managers to make informed decisions that improve workflow, enhance productivity, and reduce costs.
Solution
DMS ERP offers a robust inventory management solution for manufacturers, ensuring efficiency and accuracy throughout the inventory lifecycle.
How It Works
- Real-time Inventory Tracking: DMS ERP enables precise tracking of inventory levels and movements in real-time. This feature provides a clear view of stock quantities, locations, and status, helping prevent issues of over or understocking. Manufacturers can maintain optimal inventory levels based on current demand and production schedules, minimizing carrying costs and reducing the risk of stockouts.
- Reordering System: The system includes a simplified reordering process that allows users to see when inventory levels fall below predefined thresholds. This ensures timely reordering of materials, prevents production disruptions and enables better supply chain management.
- Integrated Inventory and Production Data: DMS ERP seamlessly integrates inventory management with production planning. This integration allows for the synchronization of material usage with production cycles, enhancing the efficiency of resource utilization. Manufacturers can accurately forecast material requirements, plan procurement effectively, and align production with inventory availability.
- Advanced Analytics and Reporting: DMS ERP provides comprehensive analytics and reporting capabilities that offer deep insights into inventory trends, usage patterns, and cost analysis. These analytics help identify opportunities for inventory optimization, reduce waste, and improve overall supply chain performance.
Many manufacturing companies face significant challenges with inefficient inventory management. Underlying issues include overstocking or understocking, which can lead to increased storage costs or production delays due to lack of necessary materials. Additionally, the inability to track inventory accurately and in real-time often results in lost items, wasted resources, and poor order fulfillment accuracy. These inefficiencies not only increase operational costs but also hinder a company's ability to respond quickly to customer demands and market changes.
Excessive reliance on manual paperwork and processes can significantly hinder operational efficiency. Manual data entry, paper-based order tracking, and physical job tickets are time-consuming and prone to errors. This often leads to inaccuracies in records, delayed processing times, and communication breakdowns between departments.
Solution
DMS ERP provides a comprehensive solution designed to drastically reduce paperwork and automate key manufacturing processes, thereby enhancing operational efficiency and accuracy across the manufacturing floor.
How It Works
- Digital Documentation and Workflow Automation: DMS ERP digitizes all essential documents and automates workflows where applicable across the manufacturing process. From digital job tickets and electronic work orders to automated invoicing and shipping documents, all information is managed electronically. This transition not only eliminates physical paperwork but also streamlines data management, ensuring that all records are accurate, easily accessible, and secure.
- Real-time Data Capture and Access: DMS ERP enables real-time data capture directly from the shop floor, using mobile devices and integrated workstations. This immediacy in data logging reduces errors associated with manual data entry and provides all stakeholders with instant access to critical information. Real-time visibility into production status, inventory levels, and order progress facilitates quick decision-making and enhances operational responsiveness.
- Process Integration and Communication: By automating and integrating various manufacturing processes, DMS ERP ensures that information flows seamlessly between departments. Real-time data keeps all relevant teams informed about production updates, inventory changes, and customer requirements, which helps in coordinating efforts and reducing bottlenecks.
- Reporting and Analytics: With reduced paperwork and automated processes, DMS ERP can aggregate data across various functions to provide comprehensive analytics and detailed reports. These insights allow manufacturers to monitor efficiency, track performance metrics, and identify areas for improvement.
DMS ERP Modules
Explore our five feature-rich modules that collaboratively address other specific pain points you may have.
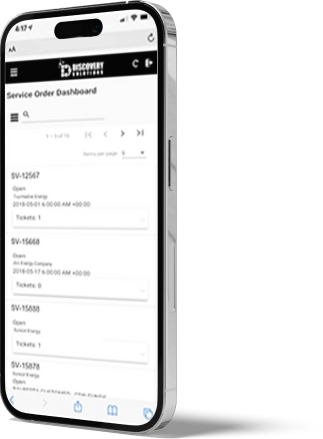
Book a Call
Schedule a quick 15-minute call and we will discuss your business challenges and if Discovery could be the right fit for you!
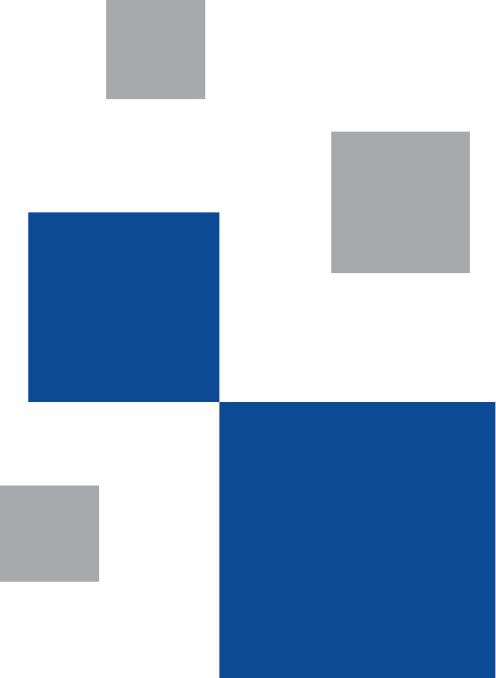